Turbo-charged development with function-oriented electrical engineering
Automation solutions up to 50 per cent faster
HEITEC Systemtechnik, headquartered near Amstetten in Austria, develops and produces automated production systems and special machinery for its customers in various industries around the world. The company’s changeover to function-oriented electrical engineering using EPLAN Electric P8 reduced development times by up to 90 per cent and increased the quality of their system documentation. All of this resulted in significantly shorter commissioning times, some of which was due to the elimination of notorious sources of errors.
Author Peter Kemptner
For the automotive, food and pharmaceutical industries, machine systems for automated production and packaging are becoming increasingly powerful, more flexible and more versatile. Despite this, these systems can never complete the entire task on their own. This requires a series of multiple machines, conveyor systems, handling devices and/or industrial robots to put together task-specific production lines. This is the domain of special machinery and production line manufacturers and automation service providers such as HEITEC Systemtechnik, based in the municipality of Ardagger in Austria.
Integrated automation solutions
The company has been a part of the HEITEC Corporate Group, headquartered in Erlangen, Germany, since 2013. It primarily develops and produces automated and often robotic-based turnkey production lines and special machinery for various industries, frequently also including integrated measuring and inspection technology. Furthermore, since 2018 HEITEC has been in a joint venture with DMG MORI, producing modular automation cells for the machine tools of this leading manufacturer.
Companies in numerous industries worldwide use HEITEC Systemtechnik solutions to increase their efficiency and profitability. Alongside the automotive industry, HEITEC is also active in the fields of electronics, logistics and aviation. The medical technology industry has also developed into a major mainstay of the company’s business. This is why certifications according to US FDA and EU Medical Device Directive guidelines are just as important to HEITEC as UL approval for the American market.
Customised development
HEITEC develops all of its customised solutions in-house, from mechanical, electrical and electronic engineering to software, the development of which goes beyond simple PLC and robotic programming. As the majority of the systems are one-offs, meaning that prototype construction is not an option, they are first created and simulated in the form of a digital twin.
For its mechanical engineering HEITEC Systemtechnik uses one of the market-leading 3D software products. For electrical engineering, the company has been using EPLAN software for many years. Because HEITEC exports the majority of its products, one of the many things the company and its employees appreciate is the ability to create language variants via translation tables and to output system documentation in accordance with the formal requirements of various international certification authorities.
“I can complete all the associated tasks using EPLAN Electric P8, from schematic creation to the placing of components in 2D,” says Marco Stressler, the electrical engineering designer at HEITEC Systemtechnik. “Looking at our low production volumes, it hasn’t been economically viable to invest in additional products to date.”
EPLAN Data Portal power user
In his work, Marco Stressler intensively uses the product data found on the EPLAN Data Portal in the EPLAN Cloud. This manufacturer-independent product catalogue provides access to product information by way of a smart search function. Thanks to the eCl@ss Advanced data standard that all the information uses as a baseline, it’s all in very high quality and depth and thus usable across disciplines.
“I can transfer the products’ mechanical characteristics from the EPLAN Data Portal directly into the mechanical engineering designs,” Marco Stressler explains. “This makes it easier to integrate components that are installed directly in the machines and helps avoid mistakes.”
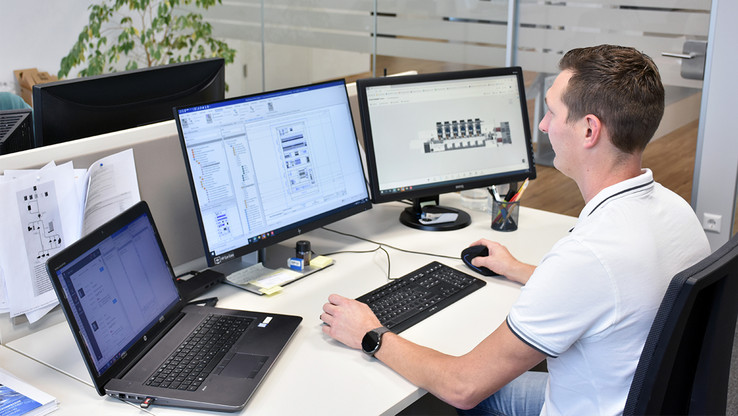
From schematic creation to placing components in 2D, the electrical engineering takes place exclusively using EPLAN Electric P8.
© Peter Kemptner
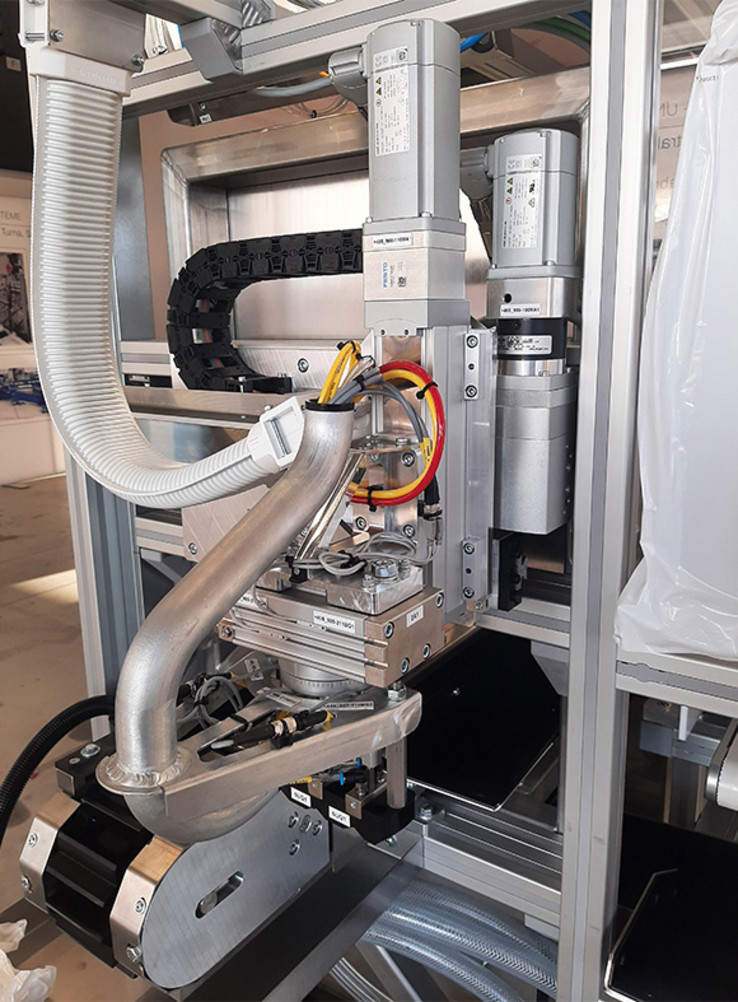
The special machinery and customised systems have a high functional density. The image shows a transfer unit with two axes and a swivelling cylinder and prism conveyor for handling medical bottles.
© HEITEC
Changing techniques in electrical engineering
There are many ways to create new projects in electrical engineering. As is the case at many companies, at HEITEC Systemtechnik it was also common practice to copy and then modify similar existing projects. In traditionally structured designs, this harbours the risk that the changes might not be applied consistently throughout a project.
“The errors resulting from inconsistent designs are, moreover, very difficult to find,” Marco Stressler says. “This enormously increases the time and labour required, particularly during on-site commissioning.”
This is why the electrical engineering designers decided to change methodologies. This meant turning away from a production-oriented structuring of the schematics, in which the document structure reflects the production sequence. Although this method has the advantage of making it possible to do the system wiring in one go, this is more than offset by the disadvantage that the functional relationships across the project are difficult to determine.
Today the electrical engineering designs at HEITEC Systemtechnik are functionally oriented. This working methodology enables the detailing of functional units, which can then be very easily combined to form complete systems.
Macro technology instead of copy and paste
“The functional units can always be seen in their entirety in one visualisation,” Marco Stressler says, talking about the most obvious difference. “While this does require a rethink when wiring, it in turn offers our technicians much better support during commissioning and troubleshooting.”
Marco Stressler uses EPLAN macros to create these functional units, which he stores in a library on the EPLAN Platform for further use. Much like object classes in software development, these are not duplicated, like they would be using copy-and-paste, but only referenced. They are given specific properties when they are integrated into a project, when the parameters are set.
Subsequent developments or changes to a macro are then available everywhere the macro is used. However, for security reasons, the update does not happen automatically. It is suggested to the electrical engineering designer, who must then confirm it – thereby avoiding any problems that could result from imprudent global changes.
Development times cut in half
Since the macros from the library serve only as references, they remain unchanged despite the parametrisation in the project and therefore cannot be accidentally altered or spoiled. The mere fact of being able to use the macros in a fully tested and finalised form accelerates development processes and makes it much easier to create variants. Added to that, the use of macros that have already been certified also considerably simplifies and shortens certification processes in a new project.
By switching to function-oriented engineering using EPLAN macros, HEITEC Systemtechnik has turbo-charged its development processes in electrical engineering. “For the first project of this kind, we had to invest around 20 per cent of the time previously estimated for a similar project in developing the macro library,” Marco Stressler says, thinking about the cost-benefit calculation. “This was rewarded by an average of 50 per cent less time spent on design and a significant reduction in efforts required for testing.”
Benefits are (also) in the details
Another significant advantage of function-oriented electrical engineering using EPLAN macros is the reduction in the time spent looking for things during commissioning and maintenance. “The increased data quality generally ensures a greatly reduced error rate,” says EPLAN Regional Sales Manager for Eastern Austria Erwin Kreuzer. “This is largely due to seemingly minor details, such as the option of having the software automatically check the individual wire labelling.”
The electrical engineering designers can completely rely on the software and no longer have to check and trace back every change in all the subplans themselves, as used to be the case. These and similar test loops now automatically eliminate the previously dreaded and tedious quality assurance work in the design department and reliably prevent traditional errors. This protects the commissioning technicians from any unpleasant surprises and additionally helps to minimise the time they have to spend on site.
Another major advantage is the ability to organise EPLAN macros in a hierarchical manner. This means that even larger subprojects, which in turn are made up of many individual project macros and subproject macros, can be saved as macros themselves and re-used as often as is required for referencing and parametrisation. “For a larger automotive plant system, I only had to design one of the ten identical robots from scratch,” Marco Stressler reports. “By saving the macro, I was able to use it for all the others as well, reducing my overall design time for the project by 90 per cent.”
Satisfied Customer
Founded over forty years ago by Richard Heindl as an engineering office in Erlangen, Germany, the Heitec Group, headquartered in Erlangen, is known for its industry prowess in automation, plant systems, special machinery, digitisation and electronics, providing solutions, products and services. It currently employs more than 1,000 people in Germany as well as in its own subsidiaries in Slovakia, Hungary, Romania, Turkey and China. HEITEC Systemtechnik in Austria develops and manufactures plant system solutions, special machinery and software solutions for the automobile supplier, pharmaceutical and machine tool industries.
Marco Stressler, Electrical Engineering Designer at HEITEC Systemtechnik GmbH:
“I think one of the biggest advantages of function-oriented electrical engineering is the consistency of the system documentation and the re-usability of integrated functions. The macros from the macro project, which were previously created and checked with test loops, can be found again in the various functions. This working methodology reduces errors and my design work is about 50 per cent faster than before.”
Erwin Kreuzer, Regional Sales Manager for Eastern Austria at EPLAN GmbH
“The increased data quality generally ensures a greatly reduced error rate. This is largely due to seemingly minor details, such as the option of having the software automatically check the individual wire labelling.”